TRANSFORMING MINING OPERATIONS
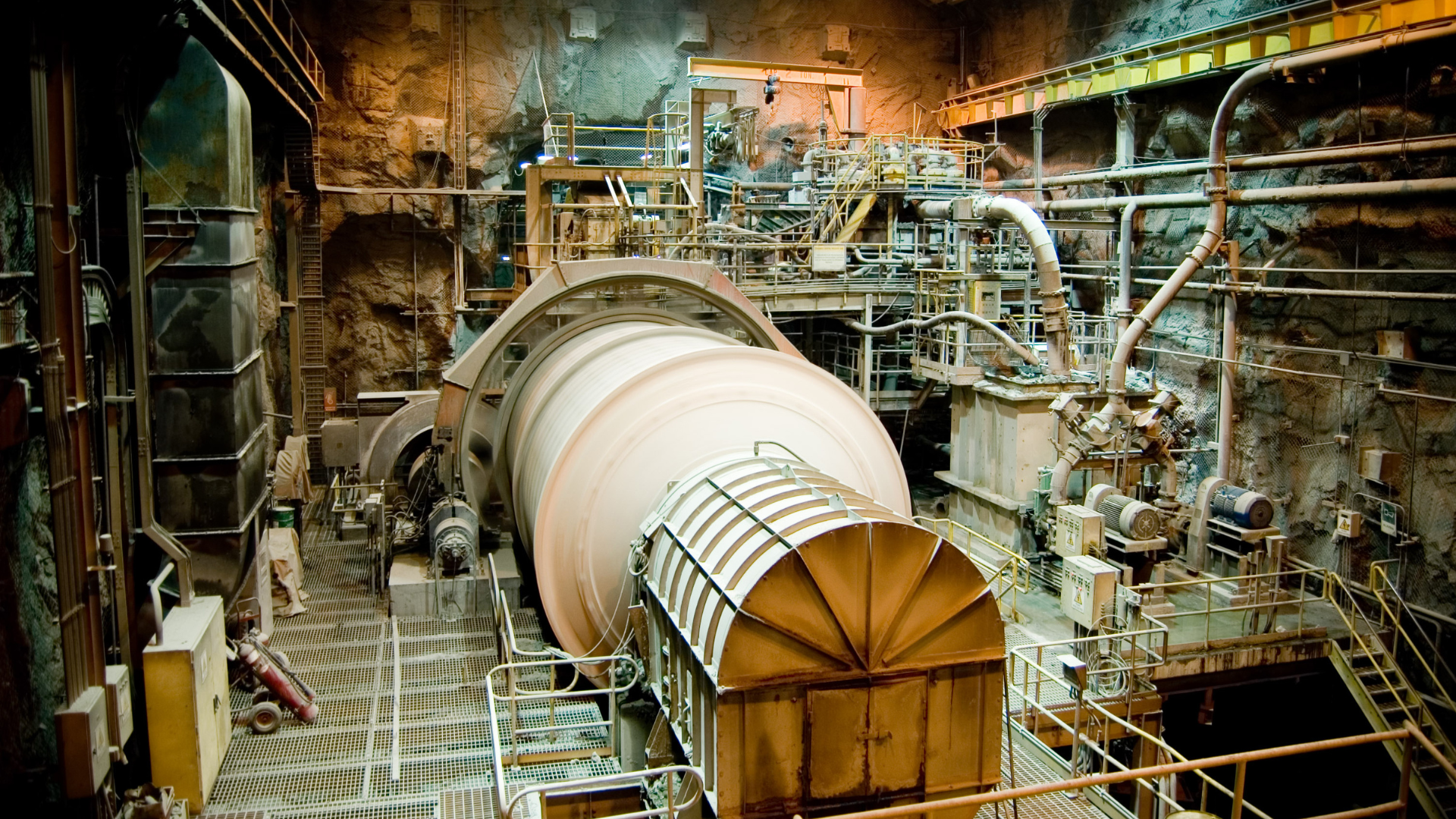
OPTIMIZATION OF A SEMIAUTOGENOUS GRINDING (SAG) MILL
Implement precise control of input variables, machine speeds, and grinding parameters to enhance throughput and process efficiency in the grinding circuit. By optimizing these factors, concentrator plants can achieve improved mineral separation and maximize the recovery of valuable minerals from the ore, leading to increased operational efficiency and profitability.
OPPORTUNITIES & CHALLENGES
-
The current control of the SAG mill grinding process was controlled by a fixed operational "recipe," which can lead to sub-optimal performance.
-
This lead to increased energy costs, higher long-term machine costs, and potential disruptions in downstream mining processes.
-
Manual adjustments alone may not fully monitor the operational process and adjust key variables such as feed, %-solids, ball diameter, and charge.
-
The challenge lies in the small volume of data available for analysis and the goal of increasing throughput while maintaining production targets.
SOLUTION
-
SentianController utilizes inferred system dynamics and prediction models to enable precise control and optimization of key variables in the SAG grinding process, including feed tonnage, water addition, mill rotation speed, and material recirculation rates.
-
The AI assistance provided by SentianController overcomes the limitations of manual adjustments, resulting in enhanced process efficiency, reduced energy costs, minimized disruptions in downstream operations, and the achievement of higher throughput and improved production targets.
HIGHLIGHTS
-
Complex optimization of large set of interdependent variables.
-
Capturing of knowledge from data and experienced operators.
-
Continuous adaptation to the ever changing system dynamics of the grinding system
OPTIMIZATION OF A GYRATORY ROCK CRUSHER
Optimize input variables, machine speeds, and crusher settings to enhance throughput and process efficiency in the crushing circuit. This optimization will enable concentrator plants to improve mineral separation and maximize valuable mineral recovery from the ore, resulting in increased operational efficiency and profitability.
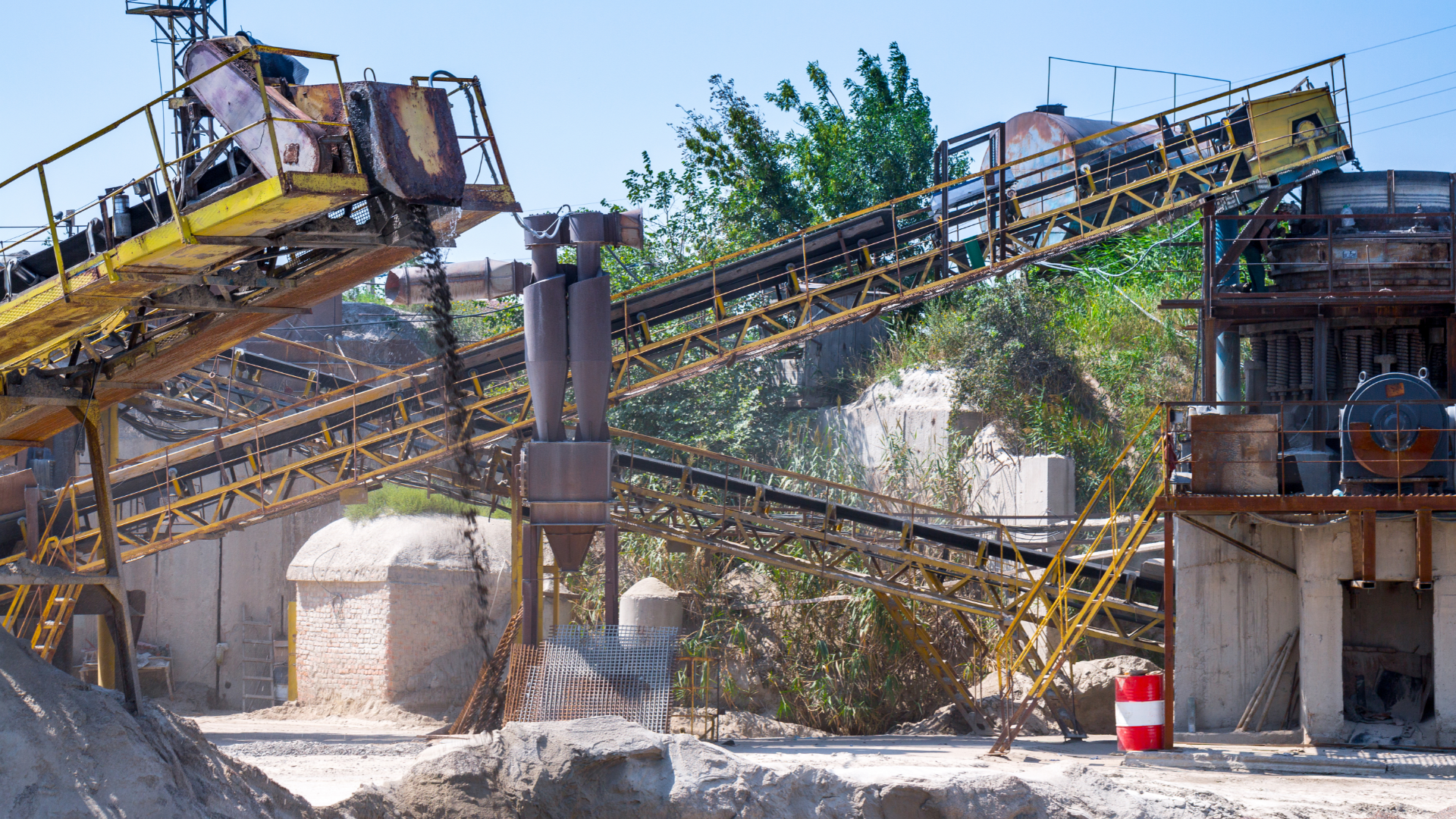
OPPORTUNITIES & CHALLENGES
-
In mining operations, the grinding process is essential for pulverizing ore into finer particles, facilitating the extraction of valuable minerals. However, sub-optimal control of the grinding process can lead to inefficiencies, increased energy costs, and diminished product quality.
-
The current approach relies only on operators who manually adjust parameters such as feed rates, mill rotation speed, and material recirculation rates. However, human intervention alone may not achieve optimal performance due to variations in ore characteristics and changing operating conditions.
SOLUTION
-
To overcome these limitations, an AIassisted solution, specifically SentianController, is implemented to optimize the grinding process.
-
The AI system utilizes historical data and real-time information to analyze ore characteristics and adjust the mill parameters accordingly.
-
It provides assistance to operators to control the feed rates, mill rotation speed, and material recirculation rates to ensure efficient grinding and particle size distribution.
HIGHLIGHTS
-
Complex optimization of interdependent variables in the grinding process.
-
Harnessing knowledge from data and experienced operators to drive improvements.
-
Continuous adaptation to the changing dynamics of the crushing system.
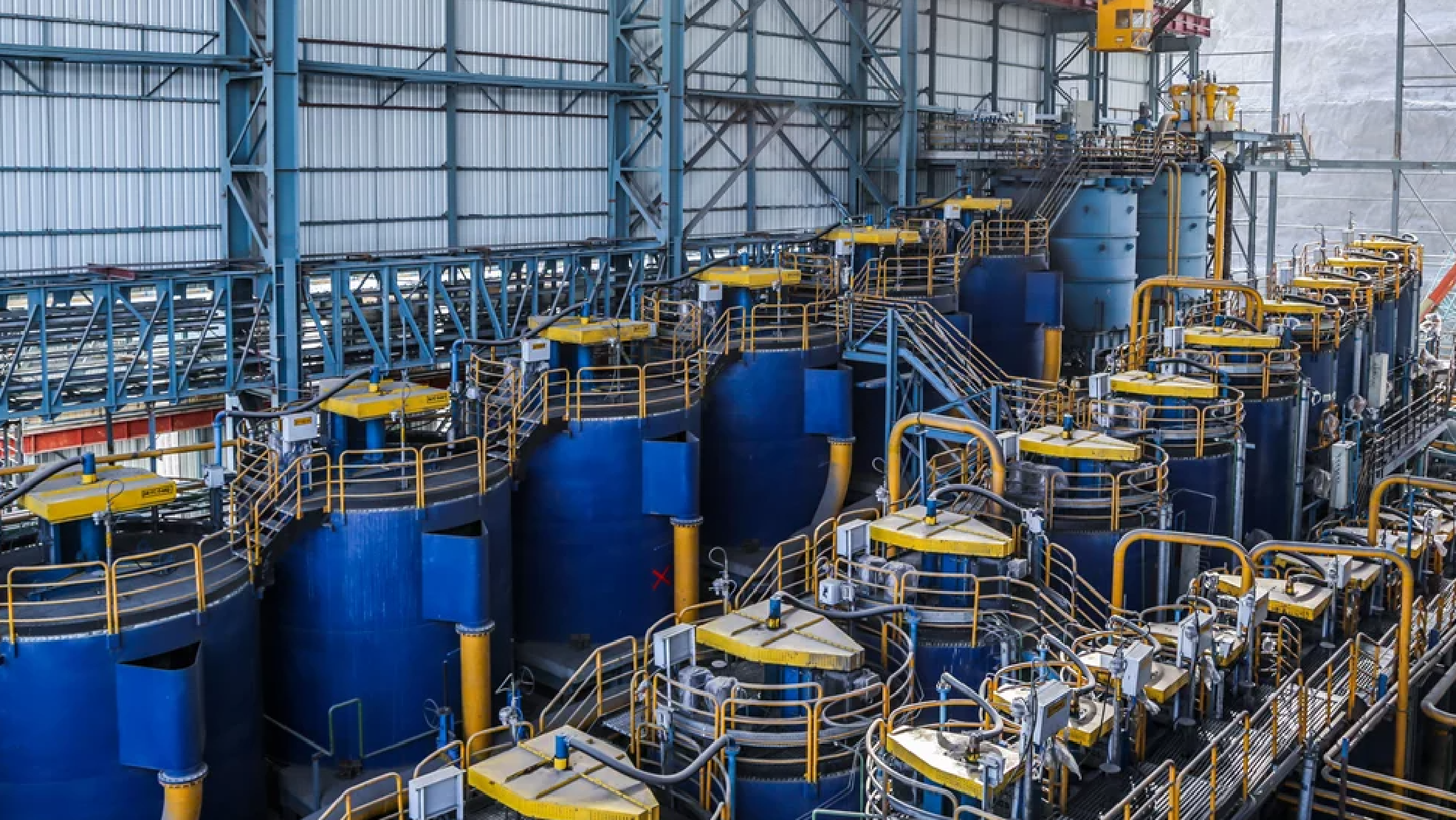
OPTIMIZATION OF A FLOTATION CIRCUIT
Establish effective control of input variables, operating parameters, and reagent dosages to enhance throughput and process efficiency in the flotation circuit. Through this optimization, mining operations can improve the recovery of valuable minerals from the ore and increase the efficiency of the flotation process, resulting in enhanced operational performance and increased profitability.
OPPORTUNITIES & CHALLENGES
-
Flotation is a critical process in mining operations for separating valuable minerals from ore. However, the current manual control of the flotation process presents challenges, such as variations in recovery and grade due to different operating philosophies among operators.
-
The process is controlled by a Distributed Control System (DCS) and operators working in shifts, but the variations in recovery and grade directly correlate with human behavior.
-
The overarching goal is to increase the recovery rate of valuable minerals, which requires addressing the limitations of manual control and human behavior in the flotation process.
SOLUTION
-
Implementing SentianController, an AIassisted solution, for optimizing the flotation process.
-
Leveraging inferred system dynamics, prediction models, and an imitation model to analyze historical and real-time data.
-
Simultaneously considering past and future information to determine the most optimal set points based on the current process state.
-
Providing operators with optimized set points and predicted process outputs to enhance their decision-making capabilities.
-
Empowering operators to maximize the recovery rate of valuable minerals through AI assistance.
HIGHLIGHTS
-
Complex optimization of interdependent variables in the flotation process.
-
Capturing knowledge from data and experienced operators.
-
Continuous adaptation to the everchanging dynamics of the flotation system.